High-performance plastic extrusion solutions for manufacturers
Wiki Article
A Comprehensive Guide to the Process and Benefits of Plastic Extrusion
In the huge world of manufacturing, plastic extrusion emerges as a necessary and highly effective procedure. Transmuting raw plastic right into constant accounts, it provides to a myriad of sectors with its impressive flexibility.Recognizing the Basics of Plastic Extrusion
While it might show up complicated at first glimpse, the procedure of plastic extrusion is essentially simple. The process begins with the feeding of plastic material, in the type of granules, pellets, or powders, right into a heated barrel. The shaped plastic is then cooled, solidified, and reduced right into preferred lengths, finishing the process.The Technical Refine of Plastic Extrusion Explained
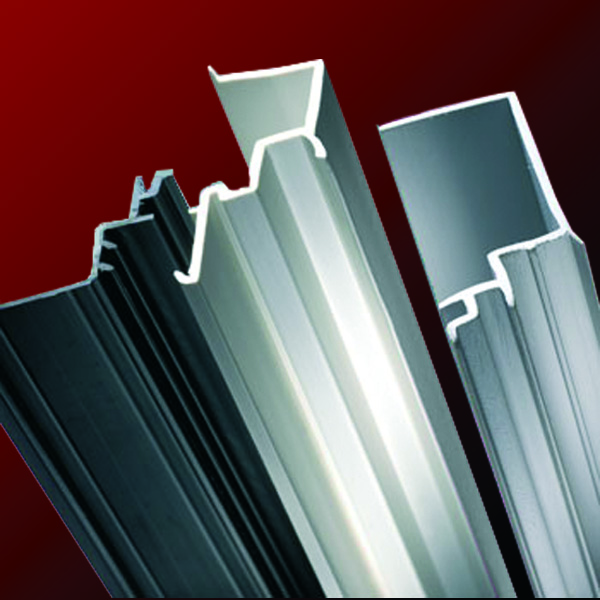
Kinds Of Plastic Suitable for Extrusion
The choice of the best kind of plastic is a vital facet of the extrusion procedure. Numerous plastics provide special residential or commercial properties, making them more suited to certain applications. Polyethylene, for instance, is typically made use of as a result of its inexpensive and simple formability. It offers superb resistance to chemicals and wetness, making it suitable for products like tubes and containers. Likewise, polypropylene is another prominent selection because of its high melting factor and resistance to fatigue. For more durable applications, polystyrene and PVC (polyvinyl chloride) are frequently selected for their strength and sturdiness. These are common alternatives, the choice eventually depends on the details requirements of the product being created. Recognizing these plastic kinds can substantially improve the extrusion process.Contrasting Plastic Extrusion to Other Plastic Forming Techniques
Comprehending the types of plastic suitable for extrusion paves the way for a more comprehensive discussion on how plastic extrusion piles up against other plastic developing techniques. Plastic extrusion is unparalleled when it comes to producing constant profiles, such as seals, pipelines, and gaskets. It likewise enables for a constant cross-section along the length of the product.Key Advantages of Plastic Extrusion in Production
In the realm of production, plastic extrusion offers several considerable benefits. One significant advantage is the cost-effectiveness of the procedure, which makes it an economically attractive manufacturing more information technique. Furthermore, this strategy supplies remarkable item versatility and improved manufacturing speed, thus boosting total manufacturing effectiveness.Affordable Manufacturing Technique
Plastic extrusion jumps to the center as an affordable manufacturing method in production. This procedure stands out for its capability to produce high volumes of product promptly and successfully, providing manufacturers with substantial cost savings. The primary cost benefit is the ability to make use of much less expensive basic materials. Extrusion makes use of polycarbonate materials, which are less pricey contrasted to metals or porcelains. Better, the extrusion process itself home is relatively simple, decreasing labor expenses. Additionally, plastic extrusion requires much less power than traditional manufacturing methods, adding to lower functional prices. The procedure additionally reduces waste, as any type of excess or malfunctioning products can be recycled and reused, offering one more layer of cost-effectiveness. In general, the economic benefits make plastic extrusion a very eye-catching alternative in the production industry.

Superior Product Versatility
Past the cost-effectiveness of plastic extrusion, another significant advantage in making lies in its premium item versatility. This makes plastic extrusion a suitable option for industries that need tailored plastic parts, such as auto, building and construction, and packaging. In essence, plastic extrusion's item adaptability cultivates development while improving operational performance.Boosted Production Speed
A substantial benefit of plastic extrusion exists in its enhanced production speed. This manufacturing process enables high-volume production in a relatively brief time period. It can producing long, constant plastic profiles, which substantially reduces the production time. This high-speed manufacturing is specifically beneficial in sectors where large amounts of plastic components are needed within tight deadlines. Couple of other manufacturing procedures can match the rate of plastic extrusion. Furthermore, the capacity to keep constant high-speed i thought about this production without compromising product quality sets plastic extrusion aside from various other techniques. The boosted manufacturing rate, therefore, not just makes it possible for suppliers to satisfy high-demand orders yet additionally contributes to raised effectiveness and cost-effectiveness. This beneficial function of plastic extrusion has made it a favored choice in various industries.Real-world Applications and Impacts of Plastic Extrusion
In the world of production, the strategy of plastic extrusion holds extensive relevance. The economic advantage of plastic extrusion, mostly its affordable and high-volume output, has revolutionized manufacturing. The sector is persistently striving for innovations in naturally degradable and recyclable materials, suggesting a future where the advantages of plastic extrusion can be preserved without jeopardizing ecological sustainability.Conclusion
Finally, plastic extrusion is a extremely effective and reliable method of transforming raw products into varied items. It supplies many benefits over various other plastic developing methods, including cost-effectiveness, high output, very little waste, and layout adaptability. Its influence is profoundly felt in various markets such as construction, auto, and customer products, making it a critical process in today's production landscape.Delving deeper into the technical procedure of plastic extrusion, it starts with the option of the appropriate plastic material. When cooled, the plastic is cut into the called for sizes or injury onto reels if the product is a plastic film or sheet - plastic extrusion. Comparing Plastic Extrusion to Various Other Plastic Forming Approaches
Understanding the kinds of plastic suitable for extrusion paves the way for a wider conversation on just how plastic extrusion piles up against various other plastic developing approaches. Couple of other manufacturing processes can match the speed of plastic extrusion.
Report this wiki page